work in process inventory formula
514 M จาก Q2 finished goods 157 M work in process ลดเลกนอย raw materials 517 M spare parts 2 M วสดสนเปลอง-แมพมพ 34 M goods in transit 209 M. Beginning WIP Inventory Manufacturing Costs Cost of Finished Goods Ending WIP Inventory.
Solved 3 Data 4 Beginning Work In Process Inventory 5units Chegg Com
Where there is opening work-in-progress in a process that is not the first stage of the production process the following special consideration is required.
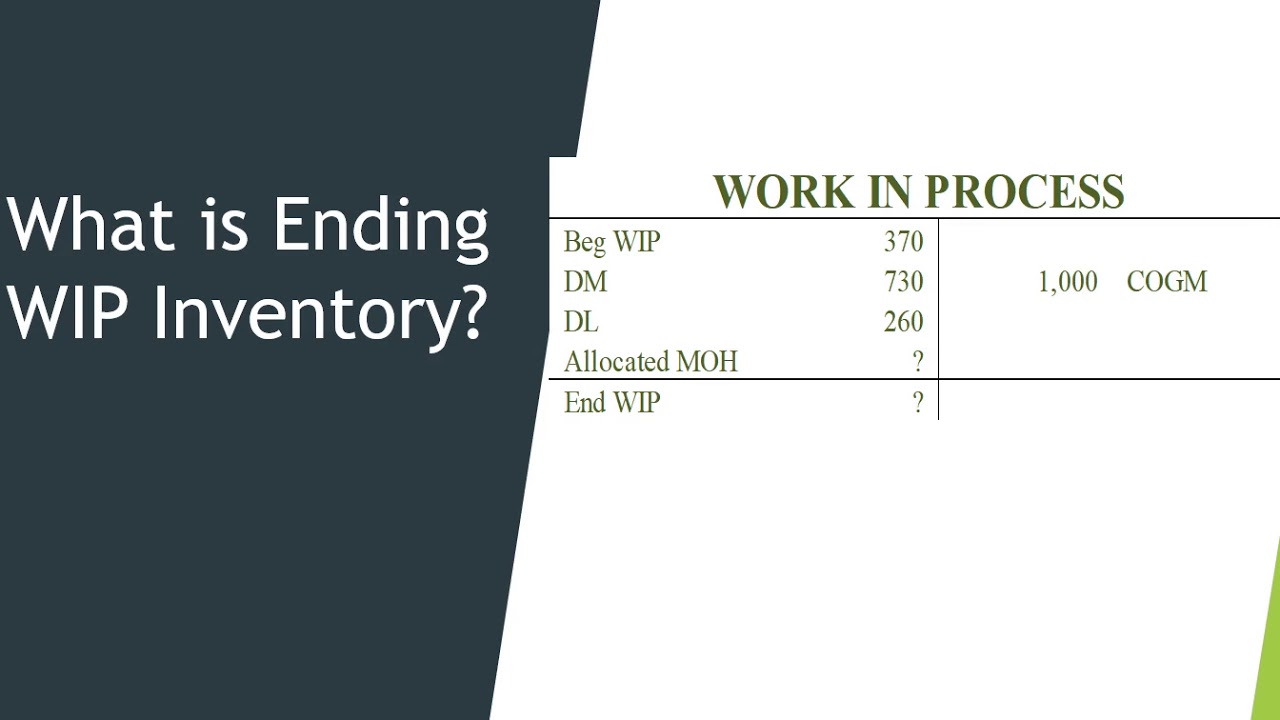
. The WIP figure indicates your company has 60000 worth of inventory thats neither raw material nor finished goodsthats your work in process inventory. WIP Inventory amount Beginning Work in Process Inventory Manufacturing Costs Cost of Manufactured Goods Work in Process VS Work in Progress. However by using this formula you can get only an estimate of the work in process inventory.
The last quarters ending work in process inventory stands at 10000. And changes in volume of production and inventory levels also tend to be small. The last quarters ending work in process inventory stands at 10000.
For the exact number of work in process inventory you need to calculate it manually. Work In-process Inventory Example. Once you have all the data mentioned.
Work in process inventory 60000. It doesnt take into account waste scrap spoilage downtime and MRO inventory. Work-in-Process Inventory Formula.
Beginning WIP Inventory Production Costs Finished Goods Ending WIP Inventory. Take a look at how it looks in the formula. Work In Process Inventory Wip.
Keep in mind this value is only an estimate. Pretend you own a hat brand and your store has a. The formula for calculating the WIP inventory is.
Work in Process Inventory Formula. Manufacturing Costs Raw Materials Direct Labor Costs Manufacturing Overhead. Each accounting cycle starts with an amount for the beginning work in process.
Work in process inventory formula. Once you know your beginning WIP inventory manufacturing costs and COGM you can start to use the WIP inventory formula. How do I account for work in progress inventory.
Inventory accounts are reported as current assets on the companys balance sheet. Total Cost of Manufacturing Beginning Work in Process Inventory Ending Work in Process Inventory Cost of Manufactured Goods. The formula for manufacturing costs is as follows.
The work in process formula is the beginning work in process amount plus manufacturing costs minus the cost of manufactured goods. 8000 240000 238000 10000. If your head is spinning with all these figures dont worry.
The formula for calculating WIP inventory is. The formula is as follows. Inventory can be finished goods Work in process goods or raw material.
After the beginning WIP inventory is determined. The value of all materials components and subassemblies representing partially completed production at plant cost for the most recently completed fiscal year. Once you have all three of these variables the formula for calculating WIP inventory is.
Assume Company A manufactures perfume. Learn how to classify work in process inventory to increase the efficiency of your inventory management operations. After the beginning WIP inventory is determined along with the manufacturing costs and the COGM its easy to calculate the amount of WIP inventory that you currently have.
Total Manufacturing Costs Beginning WIP Inventory Ending WIP Inventory COGM. Ending WIP inventory beginning WIP inventory manufacturing costs COGM. This will eventually impact the final cost of the manufactured goods.
Inventories 302 M 8181 1120 M. Works in process WIP are included in the inventory line item as an asset on your balance sheet. Ending WIP Beginning WIP Costs of manufacturing - costs of goods produced.
Definition Formula And Examples Charisma Motors is a commercial car manufacturer specializing in sedans cross-overs and SUVs. Example of the Ending Work in Process Calculation. Beginning WIP Manufacturing costs - Cost of goods manufactured Ending work in process.
The amount of ending work in process must be derived as part of the period-end closing process and is also useful for tracking the volume of production activity. The calculation of ending work in process is. To calculate your in-process inventory the following WIP inventory formula is followed.
Therefore the formula from which a business can calculate their COGM using work in process inventory costs can be displayed like this. This account represents the costs of resources used but not yet turned into completed products. This means that Crown Industries has 10000 work in process inventory with them.
If the WIP inventory is higher in the production process then the manufacturing costs like raw materials and labor costs will be higher. The difference between the sum of the beginning work in process and the costs of manufacturing is the ending work in process. Vehicles within the manufacturing plant move along an assembly.
Beginning inventory purchases goods available for sale cost of goods sold COGS ending inventory Lets assume that a sporting goods store begins the month of April with 50 baseball gloves in inventory and purchases an additional 200 gloves. Work-in-Process Inventory Formula. It is one of the inventory accounts commonly used to track the flow of costs in a production process.
Other common inventory accounts include raw materials and finished goods. The amount of ending work in process must be derived as part of the period-end closing process and is also useful for tracking the volume of production activity. Heres how youll need to do it.
How to Calculate Work-in-Progress. This means that Crown Industries has 10000 work in process. Ending WIP Inventory Beginning WIP Inventory Manufacturing Costs- Ending WIP Inventory.
Work-in-process WIP inventory turns This asset management measure is typically calculated as the cost of goods sold COGS for the year divided by the average on-hand work-in-process material value ie. In this formula COGM cost of goods manufactured. Work in process inventory calculations should refer to the past quarter month or year.
Cost Of Goods Manufactured Formula Examples With Excel Template
What Is Work In Process Wip Inventory Eswap
Manufacturing Account Format Double Entry Bookkeeping
Manufacturing And Non Manufacturing Costs Online Accounting Tutorial Questions Simplestudies Com
Ending Inventory Formula Step By Step Calculation Examples
Cost Of Goods Manufactured Cogm How To Calculate Cogm
Wip Inventory Definition Examples Of Work In Progress Inventory
Ending Work In Process Double Entry Bookkeeping
Cost Of Goods Manufactured Formula Examples With Excel Template
What Is Work In Progress Wip Finance Strategists
What Is Work In Process Wip Inventory How To Calculate It Ware2go
Ending Inventory Formula Step By Step Calculation Examples
Work In Process Wip Inventory Youtube
Solved 200 55 30 9 600 5 575 5 000 3 Data 4 Beginning Chegg Com
Cost Of Goods Manufactured Formula Examples With Excel Template
Use The Job Order Costing Method To Trace The Flow Of Product Costs Through The Inventory Accounts Principles Of Accounting Volume 2 Managerial Accounting